NCM Design Features
NCM Design Features
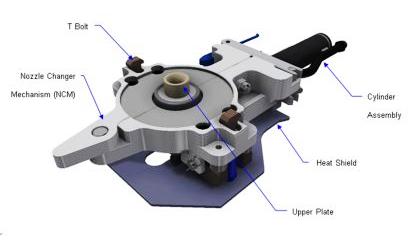
The working refractory parts of the NCM include the upper round fixed nozzle and a replaceable metering nozzle.
Two plates are kept firmly in contact with each other by the means of compression or gas springs which operate by means of a lever principle.
Springs are mounted outboard of the metal stream to prevent excessive exposure to heat and a simple adapter plate is required to provide means of attachment to the tundish bottom. These adaptor plates are welded to the tundish bottom accordingly.
NCM Cost Benefits
NCM Cost Benefits
- Facilitates longer sequence casting leading to increased production output and reduced operating costs.
- Saving on refractory costs by longer Tundish sequences.
- Saving on energy for Tundish Drying/preheating.
- Saving on production time by longer Tundish sequences.
NCM Operational Benefits
NCM Operational Benefits
- Quick nozzle changes and shut off.
- Enables Flexible production programs and high productivity.
- Nozzle clogging or wear eliminated by simply changing the metering nozzle.
- Optimum casting speeds.
- Casting speed can be changed easily by changing nozzle Bore.
NCM Safety Benefits
NCM Safety Benefits
The NCM facilitates safer plant operating practices, including;
- Individual strands can be stopped and started as required.
- Safe shut off in the event of an emergency.
- Shut off can be for an individual strand or all strands together.
- Safe shut off at the end of casting.
- Operatives can remain in a safe position away from steel flow during shut off.
- Emergency shut down can be triggered by external signals if required i.e. Mould level detectors.
- Minimal splashing due to pressurised plate contact.
- Rapid nozzle exchange minimises deviation of steel flow.
NCM Technical Features
Hydraulic Power Pack & Interface Panel
The Monocon NCM is a hydraulically operated piece of equipment, offered in standard and customised configurations. Typically the NCM includes;
- The Power pack typically utilises a 7.5Kw electric Motor which runs at 1000 Rpm.
- Normal Electrical supply is 380V 3PH 50Hz – 15 A.
- In an emergency situation all strands can be shut off by the press of a single button.
- The hydraulic interface panel contains all control systems valves and hydraulic accumulator systems required to operate the Nozzle change cylinders.
Main Control Panel
- The main control panel houses the PLC which controls all the functions of the complete system.
- Each Strand can be opened or closed from the Main Control Panel.
- Also on the main panel is an Emergency Shut off push button. Pressing the Emergency Shut - off button activates all NCM’s and provides a total shut - off of all Strands.
Strand Control Panel
- A Strand Control panel is provided for each NCM corresponding to each of the strands of the Tundish.
- The panels are located in a suitable position easily accessible by the operator.
- The specific strand panel can open or close its corresponding strand stream.
- Additionally there is an Emergency Shut off button on each strand panel to enable total shut off of all strands.